Flexible Packaging Lab Testing Sample Reports
Here at Flex-Pack Engineering we often speak with customers who have questions about what type of information they will receive in our testing reports. Following, we have compiled some sample data using a FedEx mailing envelope as a reference subject, and we performed the following tests:
- Optical Microscopy X Section using FPE as the test method and performed on an Olympus BX-51
- Fourier Transform Infrared (FTIR) using ASTM E1252 as the test method and performed on a Perkin Elmer Spectrum II
- Differential Scanning Calorimetry (DSC) using ASTM D3418 as the test method and performed on a Metter Toledo DSC2
All equipment used in these tests are calibrated annually to a NIST traceable standard, and all equipment was verified to be working properly prior to all testing conducted.
Our sample reference subject (FedEx mailer)
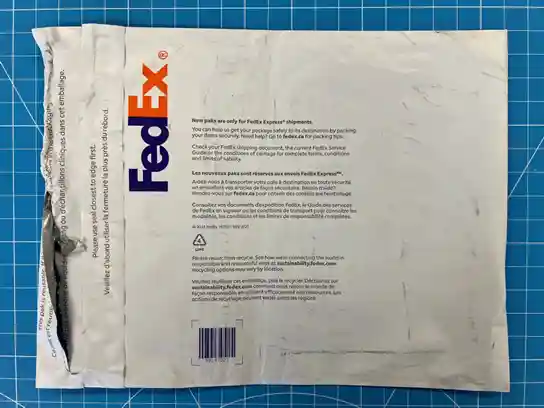
Lab Testing Results Summary
Optical Microscopy X Section using FPE as the test method and performed on an Olympus BX-51
Optical Microscopy – Visually we can only see 2 layers, 1 wide white layer (55 microns) and 1 narrow black/gray layer (20.6 microns). From experience, we know that this film structure is very likely a 3 layer coextrusion with 2 white layers (totaling 55 microns) and 1 black layer (20.6 microns). That would be white/white/black/gray. This type of product is made this way in order to increase the opacity of the film such that no documents can be read through the film from the inside to the outside of the film. In the gray/black layer of the film we can see a lot of gels, suggesting the presence of a high degree of reprocessed material being present. This would be normal for cost considerations.
Fourier Transform Infrared (FTIR) using ASTM E1252 as the test method and performed on a Perkin Elmer Spectrum II
FTIR-ATR – Using a diamond ATR attachment indicates the presence of only PE on both the inside and outside of the pouch. Normally, we would run a transmission scan as well, but due to the high loading level of TiO2 and black/gray pigment, almost all the IR light is blocked, and the resultant scan is not very useful. We can refer to the DSC to help us understand if there are any other non PE polymers are present.
Differential Scanning Calorimetry (DSC) using ASTM D3418 as the test method and performed on a Metter Toledo DSC2
DSC – Indicates the presence of 3 different polymers present. On the 1st heat we can see a small shoulder at around 110C. This is indicative of LDPE. We can also see a double peak (121.91C, 123.30C), that suggests the presence of a blend of LLDPEs. From experience, it would be normal to have multiple resins in this type of structure. (example, 1 clear LLDPE resin, 1 white masterbatch carrier resin, 1 gray/black masterbatch carrier). One or both of the carrier resins could be used as the LDPE portion of the blend + the LLDPE to increase strength. We see in the 2nd Heat that we have one broad peak at 112.83C. This can be attributed to the LDPE portion of the structure. The other peak we see at 123.18C can be attributed to the LLDPE(s). This peak is also very narrow, suggesting it is a metallocene catalyzed LLDPE (high performance).
Lab Testing Result Recommendations
If we wanted to know the % TiO2 (white pigment) we could run an Ash or TGA test. If we want to know if there is any calcium carbonate present, we could run TGA with a step analysis to sort out total TiO2 + calcium carbonate. We could also test for total carbon black content. We could also test for total Opacity and back calculate how much TiO2 and carbon black would be needed to achieve the desired opacity level and then suggest that the customer measure and adjust online while in production.
Flexible Film Packaging Testing: Results with Actionable Intelligence
The Flex-Pack Engineering team doesn’t just deliver fast test results, we offer insights and recommendations for our customers to interpret the test results and make better decisions on their flexible packaging products and processes. We contribute our 30 plus years of experience in the science and practice of flexible film packaging to our customers’ projects to improve efficiencies, save money, and get products to market faster! For a more complete list of our analytical and physical testing services, visit our Flexible Packaging Testing Services article.
Flex-Pack Engineering – Your Best Choice for Flexible Packaging Solutions
At Flex-Pack Engineering we offer competitive pricing, quick turnaround times, and thoughtful, quality driven customer service. If you are looking for product development, process optimization, testing services, or have a tough problem that you need help solving, reach out to the team here at Flex-Pack and we can help with all of your flexible packaging challenges, and solutions!
Let’s have a conversation! Call us today at 330-704-9436 or fill out our request information form.